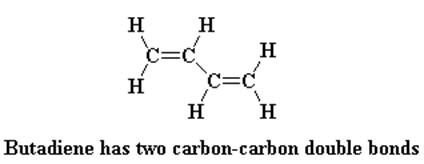
Polybutadiene
Polybutadiene was first prepared in the early years of the 20th century by such methods as sodium-catalysed polymerisation of butadiene. However, the polymers produced by these methods and also by the later free-radical emulsion polymerisation techniques did not possess the properties which made them desirable rubbers. With the development of the Ziegler–Natta catalyst systems in the 1950s, it was possible to produce polymers with a controlled stereo regularity, some of which had useful properties as elastomers.
Polybutadiene is a synthetic rubber formed from the polymerization of the monomer 1,3-butadiene. It is the second largest volume synthetic rubber produced, next to styrene-butadiene rubber (SBR), with about a quarter global consumption of synthetic rubber.
Polybutadiene has excellent abrasion resistance (good tread wear), low hysteresis loss, high elasticity, and low rolling resistance due to its low glass transition temperature (Tg), typically <−90 °C. However, this also leads to a poor wet traction properties, so, usually, BR is blended with other elastomers like natural rubber or styrene-butadiene rubber for tread compounds.
Its major use is in the manufacture of tires going into treads and sidewalls, which consumes about 70% of the production. Another 25% is used as an additive to improve the toughness (impact resistance) of plastics such as polystyrene and acrylonitrile butadiene styrene (ABS). It is also used to manufacture golf ball cores, various elastic objects and to coat or encapsulate electronic assemblies, offering high electrical resistivity.
A hard rubber called poly (styrene-butadiene-styrene), or SBS rubber is a copolymer containing polybutadiene.
Polybutadiene is a diene polymer, that is, it’s a polymer made from a monomer that contains two carbon-carbon double bonds, specifically butadiene. It is made by Ziegler-Natta polymerization.
Polymers containing 90–98% of a cis-1,4-structure can be produced using Ziegler–Natta catalyst systems based on titanium, cobalt or nickel compounds in conjuction with reducing agents such as aluminium alkyls or alkyl halides. Useful rubbers may also be obtained by using lithium alkyl catalysts but in which the cis content is as low as 44%.
Perhaps the main reason for the widespread acceptance of polybutadiene rubbers arose when it was found that they gave a vastly reduced tendency for the circumferential cracking at the base of tyre tread grooves with crossply tyres when used in blends with SBR. With crossply tyres now replaced by radial tyres, this factor is no longer of great importance but the rubbers continue to be used because of the improved tread wear and good low-temperatue behaviour imparted by their use.
Properties of Butadiene Rubber
- High Elasticity
- Low temperature properties
- Wear resistance
- Low hysterisis
- Good flexibility at ambient temperatures
- High abrasion resistance in severe conditions
- Low rolling resistance