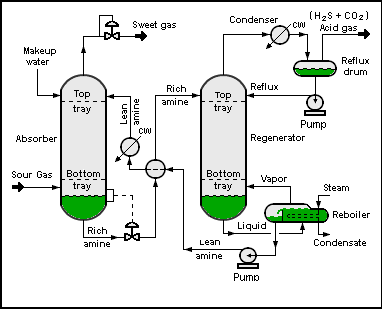
MDEA advantage in Sweeting gas process
There are many processes available for removal of contaminants from natural gas feeds. The selection of these processes is based on economic feasibility and cleanup ability. Chemical and physical solvent processes, or combinations of both, have been used extensively in many existing LNG facilities. The removal of both H2S and CO2 from natural gas before liquefaction is done primarily to meet the LNG product specifications, prevent corrosion of process equipment, and meet environmental performance standards.
Thus, purified natural gas streams prepared for LNG production should typically contain no more than 1 ppmv of H2S and 50 ppmv of CO2 Since its inception, ADGAS (Abu Dhabi Gas Liquefaction limited) has been employing the Benfield Pure process in its LNG plant in Das Island to purify sour natural gas to the above mentioned ultra-sweet specifications before it is sent to the liquefaction step.
This process that was first described by Benson and Parrish uses two independent but compatible circulating solutions in series to achieve the required gas purity. The process consists of an amine (diethanolamine) promoted hot potassium carbonate section followed by an amine (diethanolamine) section.
The choice of diethanolamine (DEA) as promoter has been underpinned by various studies that have proven DEA as the most effective promoter for potassium carbonate over others amines such as monoethanolamine (MEA), diisopropylamine (DIPA), diglycolamine (DGA), or Piperazine (PZ) Beside its relatively high capital and operating costs and high stripping energy, major process concerns of corrosion, erosion and column instability are frequently reported for units using the Benfield HiPure process in particular for the hot potassium carbonate absorber. Figure (1) shows the simple scheme of sweeting gas process.
Fig. (1). Simple scheme gas sweeting process
Methyldiethanolamine (MDEA) is a tertiary amine, which like the other amines, is used to sweeten natural gas streams. Major advantage over other amine processes:
- MDEA selectivity for H2S in the presence of CO2
- If the gas is contacted at pressures ranging from 800 to 1000 psig
- H2S levels can be reduced to concentrations required by pipelines.
- While at the same time, 40–60% of the CO2 present flows through the contactor, untreated.
- CO2/H2S Ratio, in cases where a high CO2/H2S ratio is present, MDEA can be used to improve the quality of the acid gas stream to a Claus recovery plant, but the higher CO2 content of the treated residue gas must be tolerated.
Processes use standard amines that have been combined with special inhibiting agents which minimize corrosion. Allows higher solution concentrations and higher acid gas loadings, thus reducing required circulation rates and energy requirement Utilize hot potassium carbonate to remove CO2 and H2S As a general rule, this process should be considered when the partial pressure of the acid gas is 20 psia (138 kPa) or greater. Not recommended for low pressure absorption, or high pressure absorption of low concentration acid gas.
Recent studies on methyl diethanolamine (MDEA)-based processes have shown their commercial advantages over the Benfield Pure Process in that MDEA is less corrosive to carbon steel, the solution is stable, and it is not as susceptible to degradation. Since MDEA is not very corrosive, higher concentrations of up to 50% can be used without any significant effects on the process equipment.
Also, MDEA-based processes are simple with lower capital and maintenance costs than the Benfield Pure process. However, MDEA is known for its low ability to absorb COS and Mercaptans. This disadvantage can be overcome by mixing MDEA with secondary amines such as DEA or DIPA, or an isomeric primary amine, such as DGA, known for increasing the mixture reaction rates with these sulfur and Mercaptan compounds.